BEHIND THE SCENES AT SCAPEWORKS AUSTRALIA
10 Dec 2020
The team behind Scapeworks Australia have been working hard to provide the most professional and reliable service possible. Read on to find out more.
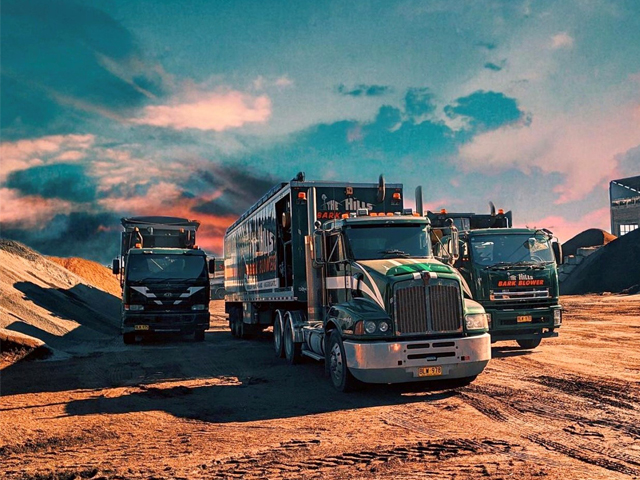
Scapeworks Australia Instagram page may look bright, attractive & sometimes glamourous, but in order to maintain its reputation and provide the level of service the team do, a lot of blood, sweat and tears goes into keeping the fleet rolling.
With unique technology often requiring parts and updates from the United States, unpredictable shipping times and varying availability of these requirements can make it tricky to ensure the mammoth fleet of 10 Blower Trucks and 4 CAS Rockslinger’s are available to deliver when called on.
Since Scapeworks was introduced to the industry in 1997, it has learnt some tough lessons over the years and like most successful businesses the team have learnt from these challenges to improve on their service. With each machine containing endless hydraulic lines, hundreds of metres of electrical wiring, thousands of bolts and fixings, along with up to 22 wheels and tyres per vehicle, there can be a lot that can go wrong on any given day which can affect the business and ultimately the service to customers. Yes, that means Scapeworks can have in excess of 220 wheels and tyres on the ground operating at any one time.
Scapeworks' ultimate goal is to provide the most professional and reliable service possible, and in order to do that it needs to ensure the equipment is operating at full strength. Though having to import many parts and pieces of equipment from the United States can be extremely expensive, the company view it as a necessity to ensure minimal downtime when issues do arise with the fleet. These days, Scapeworks ensures it has sufficient spare parts for all vehicles in stock and ready to go in the event they are required. The team have learnt over the years that being proactive and outlaying costs in advance can mean the difference between a vehicle being off the road for hours or days as opposed to sometimes weeks or months.
Operations Managers and Supervisors work tirelessly to ensure the maintenance is kept to an optimum level and that each vehicle has its required daily inspections carried out each morning before start-up.
The machinery doesn’t stop there though, with Scapeworks also incorporating 3 Volvo L150 Loaders alongside a Volvo L70 loader in order to maintain yard stock, blend project specific soil mixes as well as constantly loading the fleet throughout the day. It doesn’t matter which way you look, there are moving parts and big pieces of machinery operating constantly at The Hills Bark Blower, all vital in maintaining the supreme level of service Scapeworks is renowned for.
Like any business, some days can be more challenging than others. Whether it be extreme temperatures in summer, cold and wet winters or muddy areas after rain, the staff at Scapeworks are willing to endure these unfavourable conditions to keep the show on the road. It is not uncommon for staff to be up and into it before sun-up, as well as having to plug in the mobile lighting late in the day in order to fix an issue.
Having a strong sense of teamwork, and a good level of morale within their business makes this sometimes dirty and painful side of the service just a little bit easier to achieve.
To find out how the team at Scapeworks can help you with your next project, click on the links below.