BENDING BRIDGES
18 Apr 2019
A pedestrian bridge project, developed by a group of researchers from Mexico, features a freestanding curved wooden bridge that proposes an innovative new form for lightweight public structures.
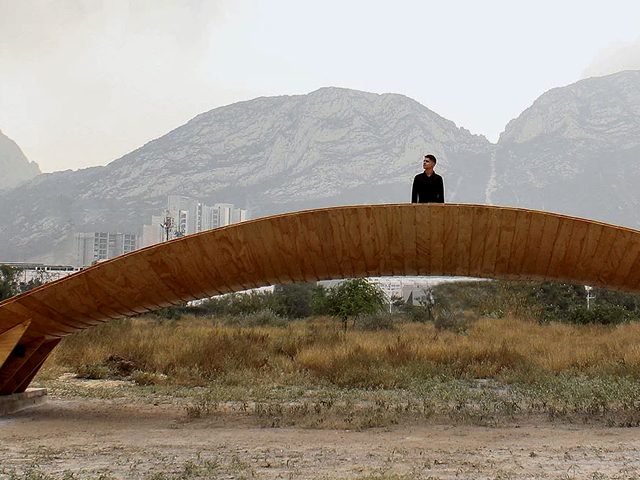
The project, Bending Bridges, developed a double-layered construction system for a free-standing load bearing lightweight wooden structure. The pedestrian bridge was achieved through global double curvature and a local active bending principle.
The bridge exploits the elastic bending capacity of standard thin plywood and proposes an innovative construction form for lightweight structures. The project was created by a group of students and research professors of the Centro de Estudios Superiores de Diseño de Monterrey in Mexico.
The design explores structurally complex curved forms that fulfil both architectural and structural constraints. The arch and surface curvature were designed and optimised through computational structural analysis to carry loads directly to the foundation. This allows the bridge to withstand the weight of five people crossing over it while guaranteeing structural integrity with minimum displacement.
The bridge’s global design has been driven by a spline-like curve, which allows it to have an optimal distribution of forces. This feature enables minimum bridge inclinations on the bottom and top of the arch. In order to allow the assembly of double-curved geometries, a set of numbered strip patterns were introduced in the design process, generating a series of unique curvilinear unrollable members.
The strategy of segmenting the bridge’s assembly allowed it to be built section by section from both ends towards the centre. The double-layer system was integrated to the process, which allowed the curvature of each section to fix in place without springback, while maintaining internal stress forces that become a stiffening factor.
An efficient wood steaming method was developed to explore heat and humidity as material treatment. The system allows to hygroscopically enhance the material bending properties enabling the assembly of a wider range of bent geometries. This makes the onsite manipulation of the material much easier. The steaming system includes a wooden box, a gas tank, a custom stove, sealed pots, stretchable aluminium pipes and a hygrometer.
All the bridge members and connections are unique, digitally fabricated with CNC machines, computationally designed in the 3D model and then materialised through CNC milling codes.
The entire construction process, programmed fabrication and assembly stages happen in parallel. Although the development of the construction system took almost a year, the project’s fabrication and construction phases took only four weeks. The final research result has a constant cross-section of 9cm, a span of 12m and a maximum height of 2.5m. The bridge presents exciting findings for the advancement of lightweight material applications and for structural performance for large span construction.
Via Designboom | Images © Héctor Pineda, courtesy of Centro de Estudios Superiores de Diseño de Monterrey